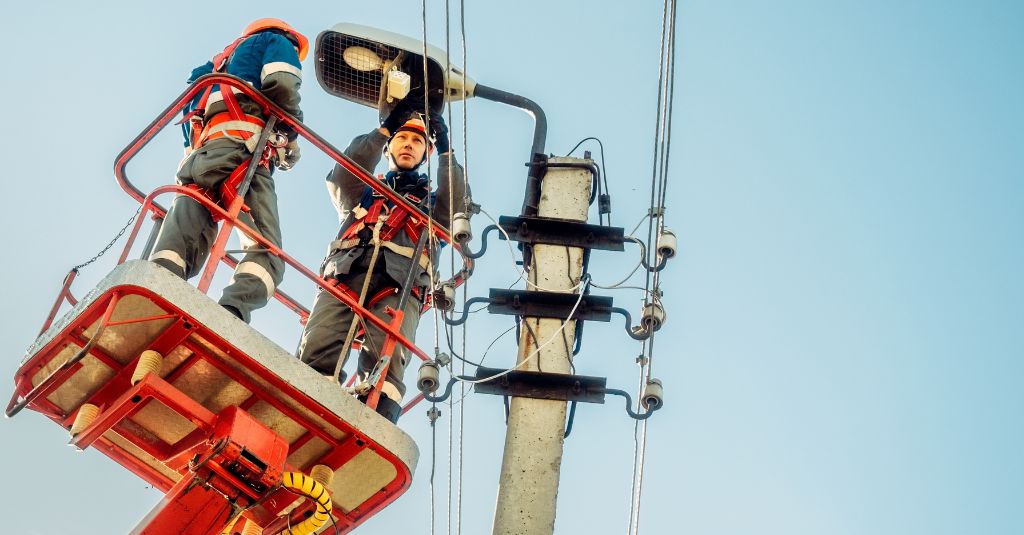
The global utility market is on a growth curve, driven by advancements in energy infrastructure. The utilities industry outlook forecasts significant changes and challenges, driven by regulatory changes, technological advancements, and market dynamics. Business Research Insights projects that the global utility services market, valued at around USD 1.65 billion in 2024, will expand to approximately USD 3.84 billion by 2033, reflecting a compound annual growth rate (CAGR) of 9.8% over the forecast period from 2025 to 2033. To achieve this growth, energy and utility providers must embrace digital transformation and overcome five key industry-wide challenges.
TABLE OF CONTENTS:
Inefficient use of personnel andenergy efficiency
Problems related to data gathering
Legacy Infrastructure
Assets, including crucial power generation facilities, are the beating heart of the utility industry and what most workers strive to preserve. The challenge in maintaining these assets is two-fold: first, many are aging rapidly and are often insubstantial to meet the needs of a changing industry. Additionally, the increasing energy demands from data centers are putting additional strain on legacy infrastructure.
Second, there is a dwindling pool of skilled labor talent that can efficiently maintain these ageing assets. Entities like smart grids are becoming a part of the everyday vocabulary in the utility industry. Electric utilities are adapting to these demands by integrating new technologies and modernizing assets to handle the significant growth in energy demand driven by emerging technologies like artificial intelligence and the shift towards renewable energy sources.
However, integrating physical assets or operational technology (OT) with information technology (IT) remains a struggle for many companies. Most are left grappling with this question: How do we modernize our assets without reinventing the wheel?
Predictive maintenance of assets is one of the key advantages the industry can harness through digital transformation. For instance, sensor-driven data helps workers tell when assets are about to fail so they can use their time more efficiently.
Rugged mobile devices are critical platforms for accessing data and making decisions on the field. Even the status of the devices themselves can be closely monitored. For example, technology such as Getac Monitoring allows repairs and upgrades to be made proactively rather than reactively.
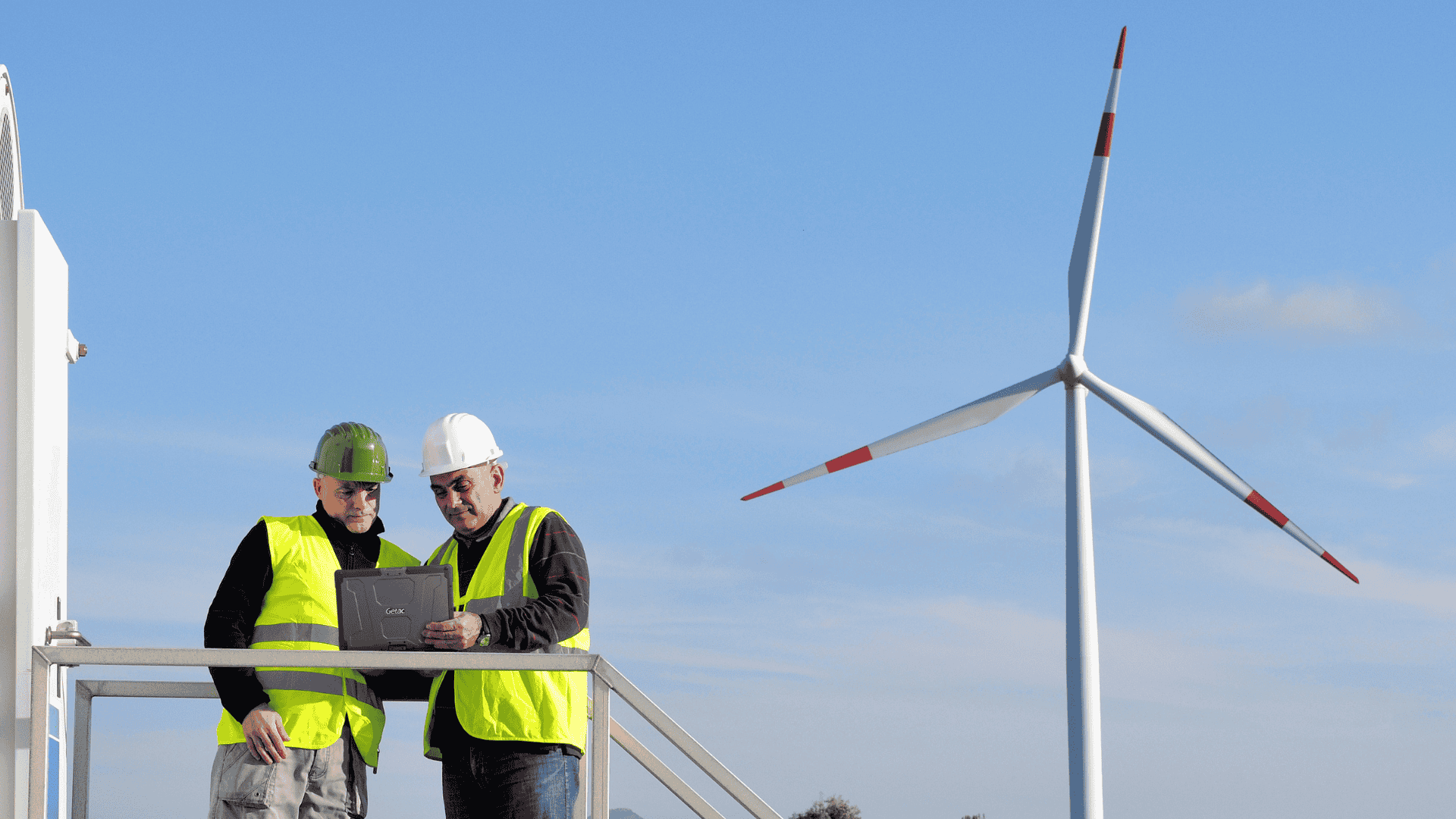
Inefficient Use of Personnel and Energy Efficiency
The utility industry workforce faces the constant challenge of stewardship of assets, which can be difficult. In addition, they must collect valuable data about assets for their industrial customers, a job that might not be their primary focus. Field services have always been the company’s face, but that job has become more complicated in today’s customer service environment. Customers are getting more demanding and need faster service, increasing the pressure on the workforce.
Moreover, the utility industry must also deal with decreasing profit margins and decreasing availability of skilled talent. Utility companies must ensure the right person is being dispatched efficiently on the right job at the right time.
The industry is changing rapidly, with varying energy sources coming from renewables and traditional sources. These, combined with digital transformation and the smart grid and smart meters, mean organizations must quickly ramp up worker training. Rugged mobile devices on field sites help workers handle the frequently evolving challenges of their job.
Improvements in energy efficiency can help manage the increased energy demands and reduce the burden on the workforce.
One exciting advance in employee training involves virtual reality (VR). Detroit-based energy company DTE Energy harnessed VR to train employees in high-consequence scenarios from the safety of their office. This includes operating at great heights, repairing down wires, and shutting off gas lines.
Problems Related to Data Gathering
The modern digital transformation of the utility industry – dubbed Industry 4.0 – could reasonably run on data. Too often, there is excessive redundancy in the data collection process. Antiquated protocols mandate workers to gather the same data repeatedly for input in various data management systems.
Such procedures keep workers away from the real job of attending to assets and increase frustration. Many companies still rely on pen and paper, which is also not the most reliable method of data-keeping. As a result, workers must transfer data from one format to another. This wastes time and increases the potential of introducing errors.
The utility industry challenges also manifest in other ways. With digital transformation in place, sometimes companies end up drowning in too much data from too many assets, primarily due to data center demand. It isn’t easy to know which data to focus on and what they tell us.
Centralized asset management systems and digitized information help make sense of the data gathered. Mobile devices are critical in accessing the correct data at the right time. This enables field service workers to make decisions efficiently and return broken assets to the grid faster.
Software solutions are arising to help utility companies gather better-quality data. One example is FlexiBill, developed by the New Zealand company Flux Federation. This software enables energy retailers to handle increased data volumes to price cleaner energy forms effectively.
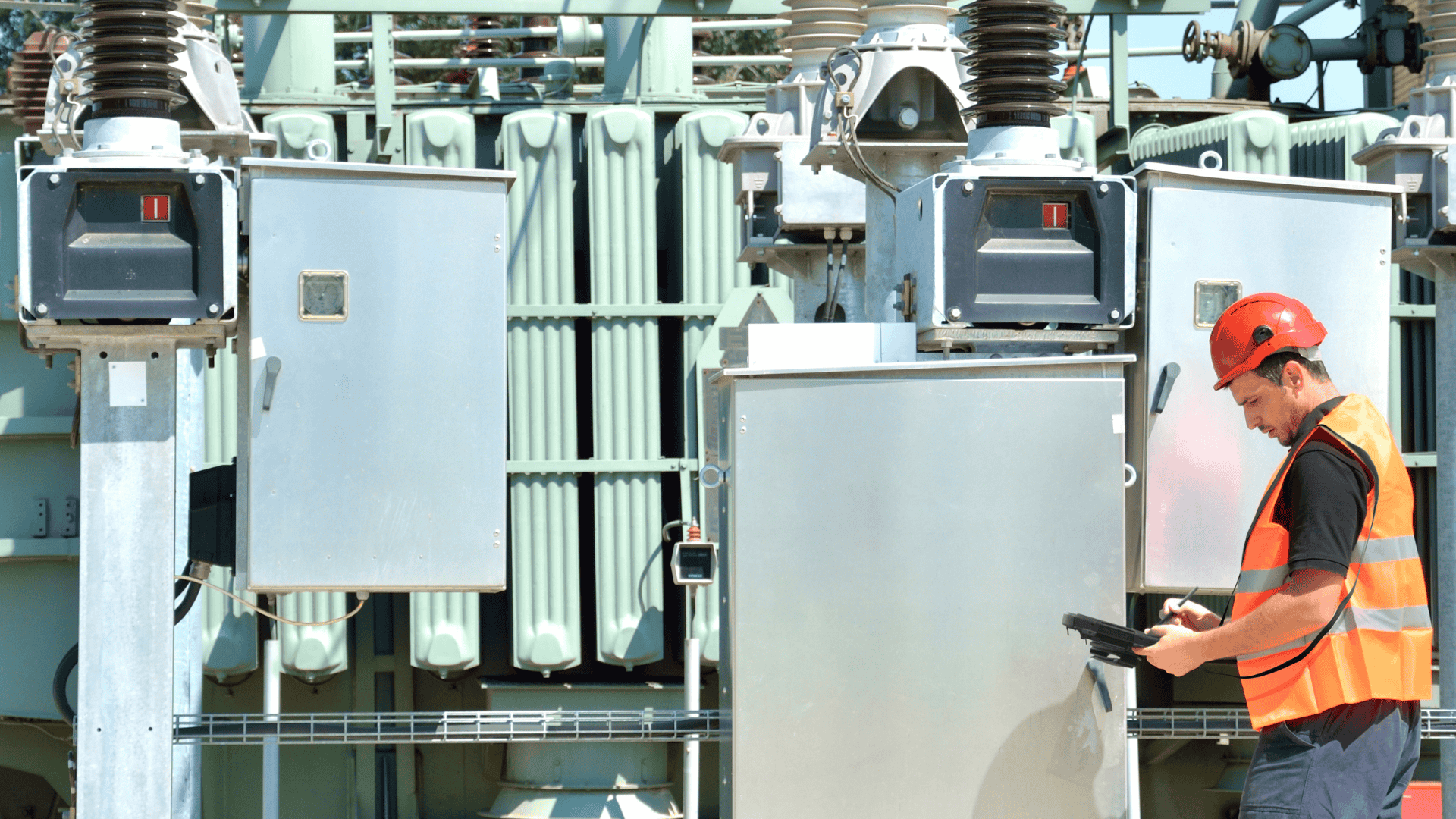
Disjointed Communication
It is essential to have consistent communication between the onsite worker and the dispatch or home office. Too often, each person works with a different set of information, leading to confusion and delays in asset management.
The rising power demand necessitates efficient communication between onsite workers and the home office to ensure timely responses and grid reliability.
Everyone is on the same page when workers use rugged mobile devices with the appropriate enterprise asset management (EAM) and enterprise resource planning (ERP) software. Workers can have real-time access to information. The bonus of having real-time data is delivering better customer service. Workers can update customers seamlessly about the status of repairs.
Canadian energy utility Spark Power introduced a mobile app solution to bolster communication across their operations. This app is spread over 35 locations in Canada and the United States. Keeping employers informed and engaged in the face of a vast geographical scale is a common challenge for utility providers. Better technology, hardware, and software lie at the heart of the solution.
Unpredictability
The uncertainty of extreme weather and natural disasters can cut off access to assets for extended periods. These problems lead to increased reactive maintenance and responses by field workers. At the same time, worker safety in heavy industries is paramount. Dispatch and workers must balance the need to get utilities back up and running with safety and access challenges.
Natural gas plays a crucial role in balancing renewable energy sources and supporting grid reliability during unpredictable events.
Digital transformation is helping utilities stay ahead of the curve with predictive maintenance of assets that might be about to fail. This allows the workforce to stay on top of emerging problems before they worsen. Mobile devices likewise play a critical role in accessing data and the correct information while on the road. Intrinsically safe tablets are essential in ensuring workers’ safety in hazardous environments.
Energy Transition and Grid Resilience
The energy transition is reshaping the utilities sector, strongly emphasizing reducing greenhouse gas emissions and bolstering grid resilience. Renewable energy sources, such as solar and wind power, are set to play a pivotal role in meeting electricity demand, with projections indicating they will account for 50% of the market in 2025.
To navigate this transition, utility companies are making significant capital investments in new technologies, including artificial intelligence and data analytics. These advancements are crucial for improving efficiency and reducing operational costs. However, integrating renewable energy sources into the existing grid presents a formidable challenge, necessitating substantial investments in grid capacity and energy storage solutions.
Independent power producers are emerging as key players in the energy industry, introducing new competition for traditional utility companies. This shift is driving utility providers to innovate and adapt, focusing on delivering more personalized and efficient energy services to their customers.
Artificial intelligence and data analytics are at the forefront of this transformation, enabling utilities to enhance customer engagement and offer tailored energy solutions. These technologies also play a critical role in managing grid operations, improving resilience, and minimizing the risk of power outages.
Utilities firms are investing in advanced weather forecasting and predictive maintenance technologies to further enhance grid resilience. These innovations help anticipate and mitigate potential disruptions, ensuring a more reliable energy supply.
The energy transition presents a significant opportunity for utilities to drive growth and enhance their competitiveness. However, it also demands substantial investment and continuous innovation to successfully navigate the evolving landscape of the energy and utilities industry.
A Data-Rich Future
Real-time information is critical for field workers to do their jobs efficiently and quickly.
The energy and utility industry is facing many complex challenges. Mobile devices help workers address these challenges efficiently.
Rugged mobile devices also facilitate all kinds of work in utilities. These include vegetation mapping and management, smart water reading, surveying, and GIS tasks. These jobs, too, have pain points mobile devices can address well.
Frequently Asked Questions
What are the critical challenges of the utilities sector?
The utility sector is hampered by dated infrastructure, inefficient labor usage, data-gathering challenges, poor communication, and the industry's unpredictability.
What is one current industry trend in energy and utilities?
A move towards automation is one significant trend. In recent years, we have seen significant technological advances like Internet of Things (IoT) devices recording measurements that once were manual.
How can the energy industry be improved?
A widespread reliance on legacy processes can become a significant barrier to efficiency. Data collection is typically manual, and technological solutions are often applied on the wrong initiatives. Addressing these areas could see significant efficiency gains in the energy sector.
What is the future of utilities?
The utility sector will continue growing with population, but many components will rapidly change in the coming years. The utilities industry outlook anticipates significant developments and challenges in the coming years. These include regulatory changes, technological advancements and innovation, and evolving market dynamics with new entrants competing for market share. The move from legacy energy systems towards renewables is an opportunity for growth and competitive advantage. It will be critical for new and existing companies to know and adapt to technological trends to maintain and grow.
Subscribe to our newsletter
Subscribe below to be kept up to date on the latest industry and technology trends. We will send you a monthly blog round-up direct to your inbox.