Getac F110 and T800 optimise processes in the marine and port sector
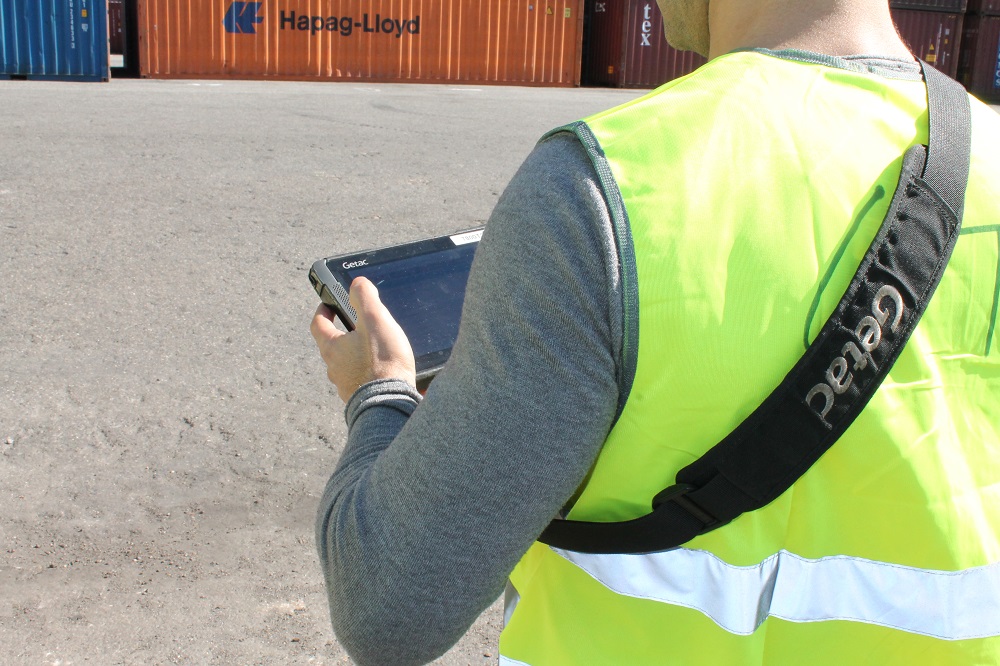
/ Challenge / (Summary)
The Genoa based Spinelli Group is the leading Italian provider of port and intermodal transport logistics solutions; it needed to find a rugged and reliable solution to manage the information flow digitising process between the port terminal and Head Office. The loading and unloading of ships and container transport are fast-paced operations taking place outdoors, under difficult conditions, in all kinds of weather, and at any time of the year. Both reach stacker operators and ground handling staff needed lightweight, easy-to-operate, technologically advanced devices to send and receive in real time all the necessary information to manage the flow of both inbound and outbound data.
/ Solution / (Summary)
After testing numerous rugged hardware solutions, the company settled for Getac's Fully Rugged F110 and T800 Tablets, which proved to be the ideal choice in terms of reliability and efficiency in a critical environment such as a port terminal, where risk factors such as wind, rain, salt, humidity, and extreme temperatures can greatly affect daily operations. Both the 8" screen of the T800 and the 11.6" screen of the F110 are perfectly readable in sunlight or in the rain, can be used while wearing work gloves, operate both at high and low temperatures and ensure excellent WI-FI and 4G/LTE connectivity, which is essential for data transmission in an environment where poor reception is likely due to container stacks stored inside the port area.
/ Benefits / (Summary)
The F110 tablet installed in the reach stackers on a dock station, and the T800 provided to operators with a support belt so they can work hands-free, along with the software solution developed in-house by the Spinelli Group, have simplified and sped up data reception and transmission methods from the port area to the Group's headquarters, and vice versa. In the past, these activities were performed entirely manually with paper and pen, with the risk of incorrect copying. Digitising the data transmission process has allowed the Spinelli Group to significantly reduce the amount of time for each task, which is absolutely crucial to the efficiency of logistics and transport management in port areas.
/ Challenge /
For over 50 years, the Genoa based Spinelli Group has been a national logistics provider in the marine and ports industry, offering a wide range of services covering the entire logistics chain, from port terminal to intermodal transport, transportation by lorry to warehousing and storage, including container sales and repairs. In the port sector, the Group manages the Genoa Port Terminal, an area of 150,000 square meters where it is responsible for the handling, storage, loading/unloading of containers, as well as weighing and lashing special loads on behalf of major shipping companies.
The Genoa Port Terminal handles over 580,000 TEUs each year, to and from
North Africa, Turkey, Israel, Canada, North America, Central America, South America, Island of Malta, Sicily and Sardinia for Italy.
A few years ago, in order to meet the efficiency requirements of the market and of shipping companies, the company began a process of reorganisation and computerisation of processes, with the aim of improving productivity in the terminal and speeding up data transmission procedures between the head office, customs and the port authority system. At the same time, there was a need to find a technology partner for Hardware Solutions, capable of ensuring seamless operations. Goods are always handled outdoors in port areas, often in adverse weather conditions, such as in heavy rain or direct sunlight. In addition, salt, humidity and wind are factors that further aggravate the outdoor working environment for operators, who must be able to rely on robust, reliable devices that are easy to operate and shockproof, in order to more quickly manage the high flow of information and incoming and outgoing data. All these factors have contributed to the demand for a rugged hardware solution compatible with the Spinelli Group's in-house software, in order to develop a solid platform, both technologically advanced and user-friendly for all staff involved in the intermodal logistics chain.
/ Solution /
To find the right technology partner, the Spinelli Group turned to its IT partner, Genoa based Sanval, which involved Getac in the initial product field-testing stage. Sanval, along with Getac, have come up with the perfect solution based on the Fully Rugged F110 tablet and vehicular dock for the reach stacker, and the Fully Rugged T800 Tablet with an 8" screen for ground handling staff, who need to use hands-free tablets. Since 2015, both devices have proved to be ideal for the group's needs in terms of being easy to handle and on account of their size, weight, security and robustness. The LumiBond® 2.0 innovative technology allows for readability in bright sunlight, and the touch screens can be used while wearing work gloves, while its excellent WiFi and 4G/LTE connectivity is essential for operators working in a port environment full of stacked containers, causing reception disturbances, interference and connection problems. The F110 Tablet combined with the vehicle Dock installed inside the reach stacker cabin enable operators to process data independently, while the T800, used by ground handling staff, is lightweight and easy to operate, with has a slim and ergonomic design, while the non-slip surface makes it easy to hold. The 16:10 screen ratio and 170° viewing angle make it ideal for reading from any angle, perfect for outdoor working conditions.
/ Benefits /
Spinelli port operating staff needed high-performance, technologically advanced devices, for the high data traffic managed in loading and unloading containers, as well as in monitoring the situation on board the ship and inside the containers. Getac's fully rugged F110 and T800 tablets have proven to be the best option, as well as fully meeting the needs of operators and technicians working outdoors, since they conform to specifications for use in adverse weather conditions, and are perfectly compatible, thanks to the use of advanced Windows 10 standards, with the TOS (Terminal Operating System) developed in-house by the Spinelli Group, managing data between the terminal, E-PORT, head office and customs. The efficiency of a port terminal is determined by the ability to organise the loading and unloading of containers and completion of related customs procedures as quickly as possible, so as to let the ship depart immediately for the next stage of its itinerary without slowing down its progress. In the past, all these processes were managed in paper format, with the risk of copying and reporting errors that actually slowed down all tasks. In order to improve performance and become an efficient and competitive player on the international market, the Spinelli Group began a review of its organisational models over ten years ago and underwent a process of reorganisation and digitisation of all its activities. In addition, efficient work flows are guaranteed by Getac's after-sales services and a bumper-to-bumper warranty, which deals with faults as well as accidental damage, thus minimising product downtimes.
"Today's shipping companies require an efficient and highly organised port logistics platform, and thanks to innovative suppliers such as Getac, we have been able to provide increasingly efficient services for our customers. Being an innovative company in providing services for the port sector and ensuring high-quality standards at all times based on skills and professionalism is one of our our main objectives” states Ivo Bonomi, ICT Manager of the Spinelli Group.
"Thanks to our technology partner, Sanval of Genoa, which has continually supported us in this process of innovation, we have identified the fully rugged Tablets F110 and T800 by Getac as the most appropriate products to support our technologies. Our operators, both in the reach stacker cabin and the ground handling staff, can manage all loading or unloading stages independently while keeping to the schedules and adhering to the correct operating methods, without fear of work interruptions due to adverse weather conditions, and actually improving the efficiency of their day-to-day tasks".
/ About SANVAL SrL - Genoa /
The partnership between Getac and the Spinelli Group began thanks to Sanval, a company based in Genoa specialising in the supply of industrial automation and network management systems, which has found in Getac's fully rugged devices the perfect solution to facilitate the work of employees who need to work outdoors.
A company operating in the distribution of electronic and electromechanical components, specialising in the production of optical cabling, design and supply of components and systems for industrial Ethernet networks and creating customised solutions in the field of industrial computing. It is recognised as a valid partner for the supply of hard-to-source products. The company operates mainly in the process automation sectors, in the marine and railway industries, telecommunications industry and military sector.